Made for
If you need larger plastic parts we can make it happen.
Vacuum forming has become a popular production method due to the rapid advancements in forming, machining, and material technology. It is increasingly being used in various applications as it offers high strength, formability, and design flexibility.
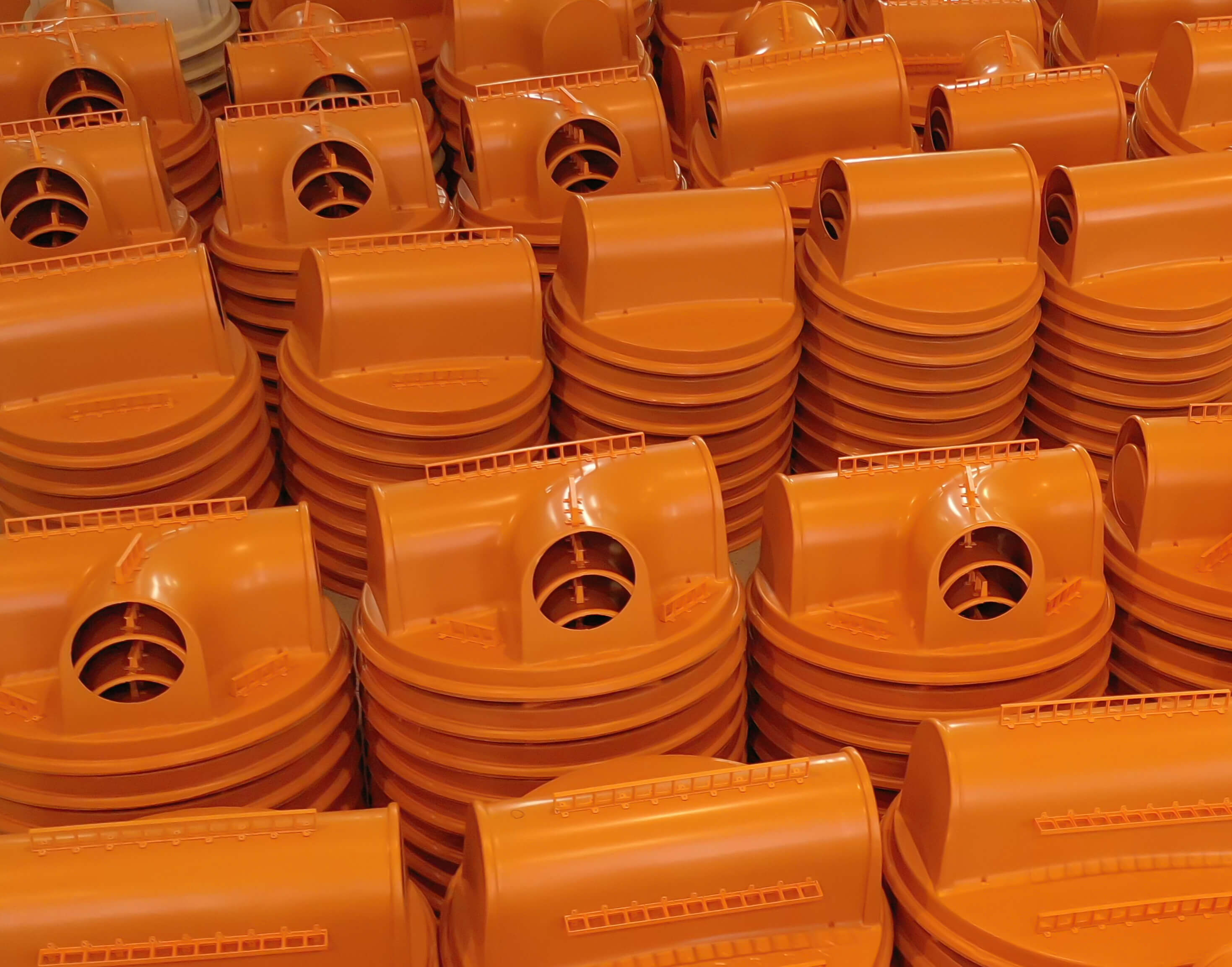
Key advantages of vacuumforming technology
In many cases, vacuum formed plastic products can replace entire assemblies made from different materials, such as metal or composites, resulting in better products at lower costs.
Vacuum forming is often the preferred option for producing physically large articles with complex shapes and extensive surface finishing requirements. This is because the process offers greater flexibility in terms of design and tooling options, resulting in high-quality products that are both cost-effective and aesthetically pleasing.
One key advantage of thermoplastics is that they are recyclable and environmentally friendly, making them a sustainable and eco-conscious choice for manufacturers.
Additionally, thermoplastics are lightweight, durable, highly impact-resistant, chemical-resistant and wear-resistant and have a long lifespan, therefore ideal for use in a variety of products and applications.
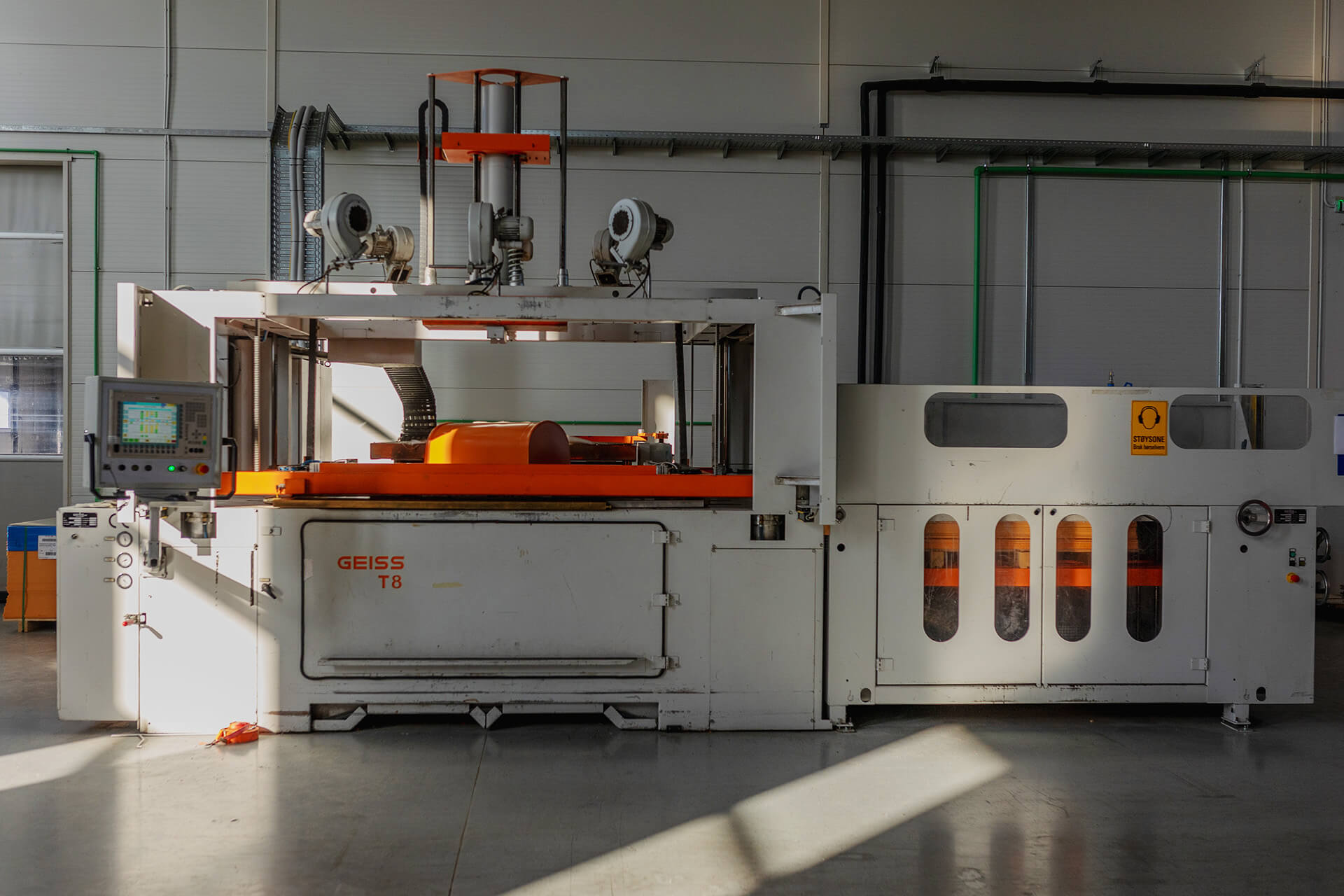
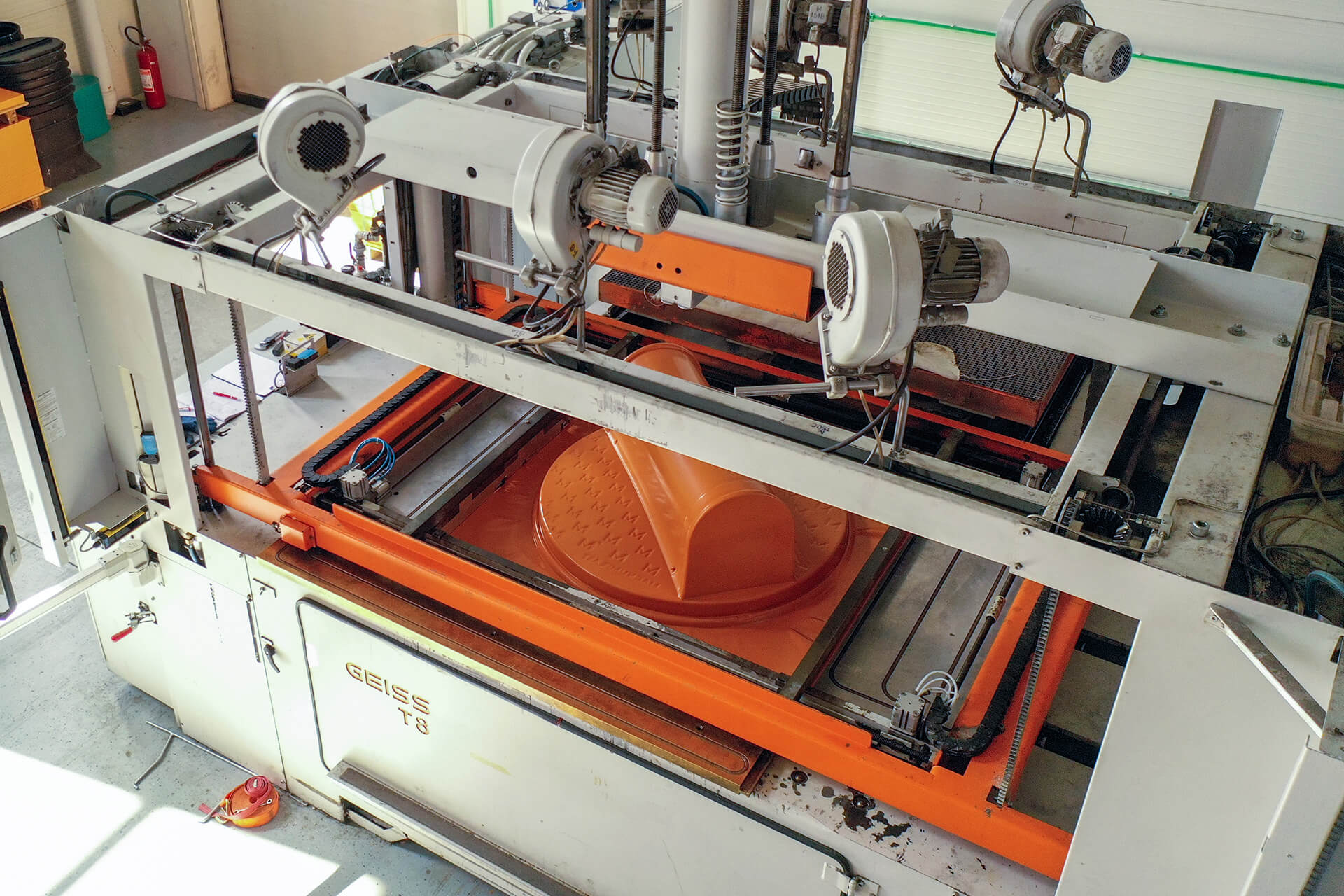
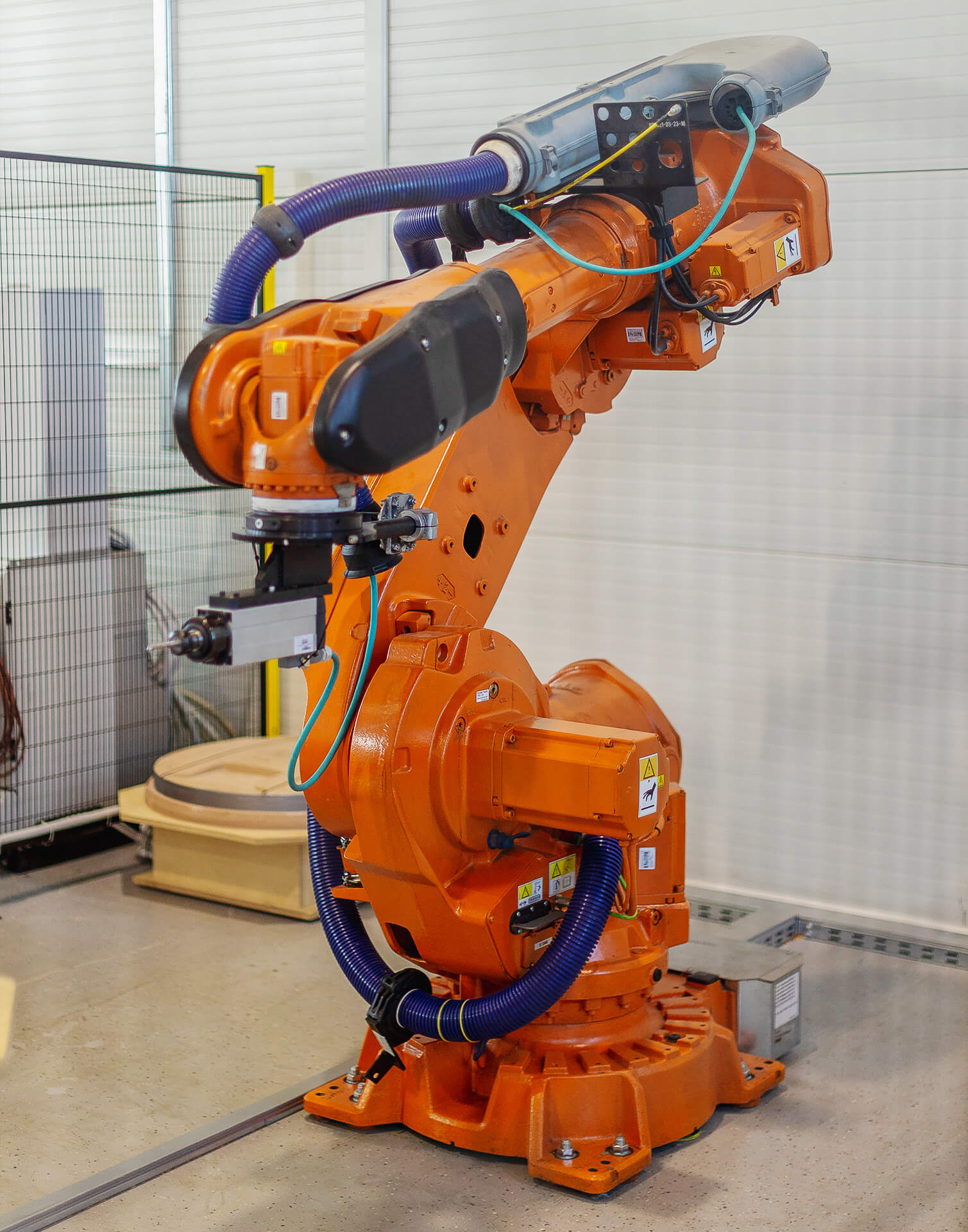
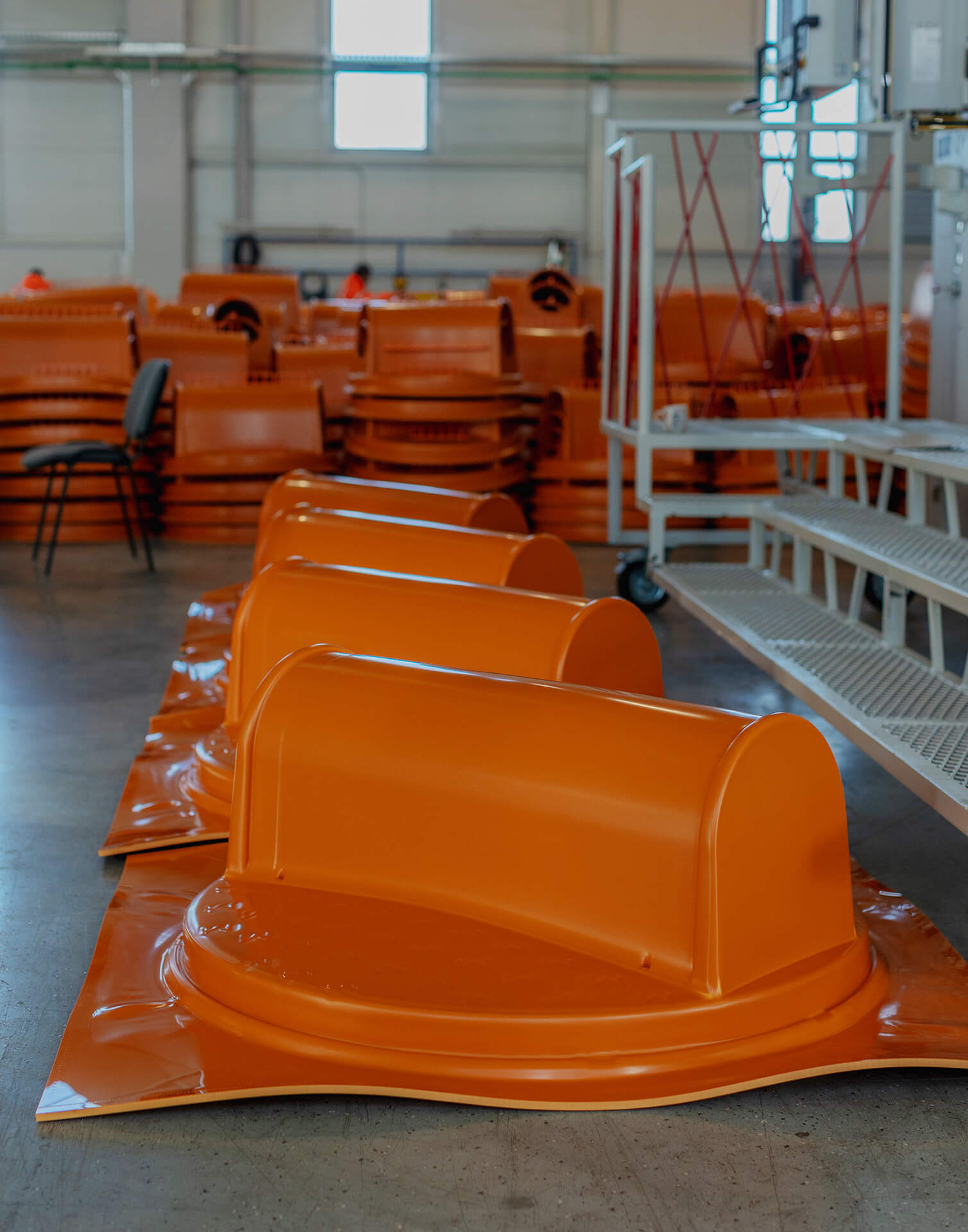
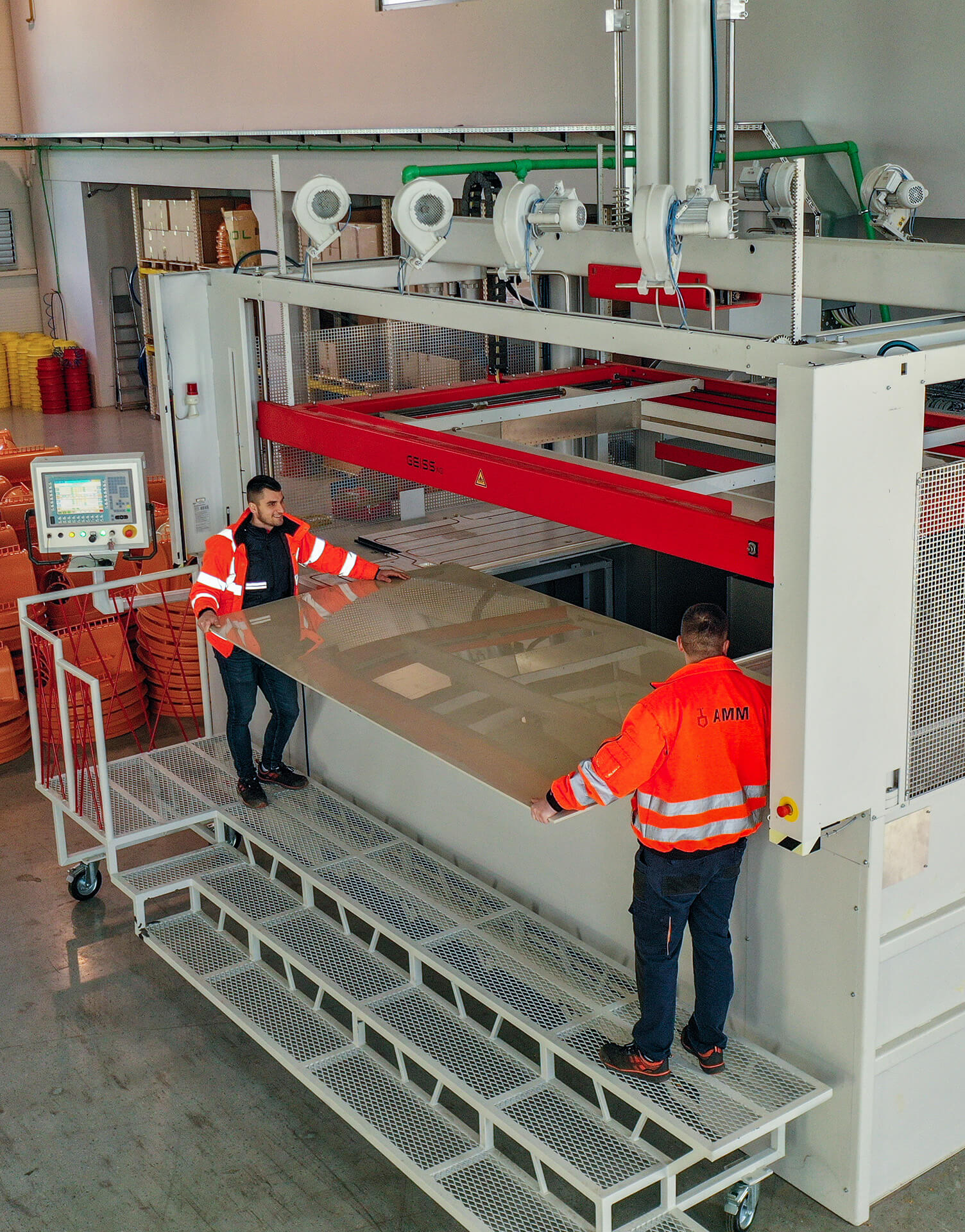
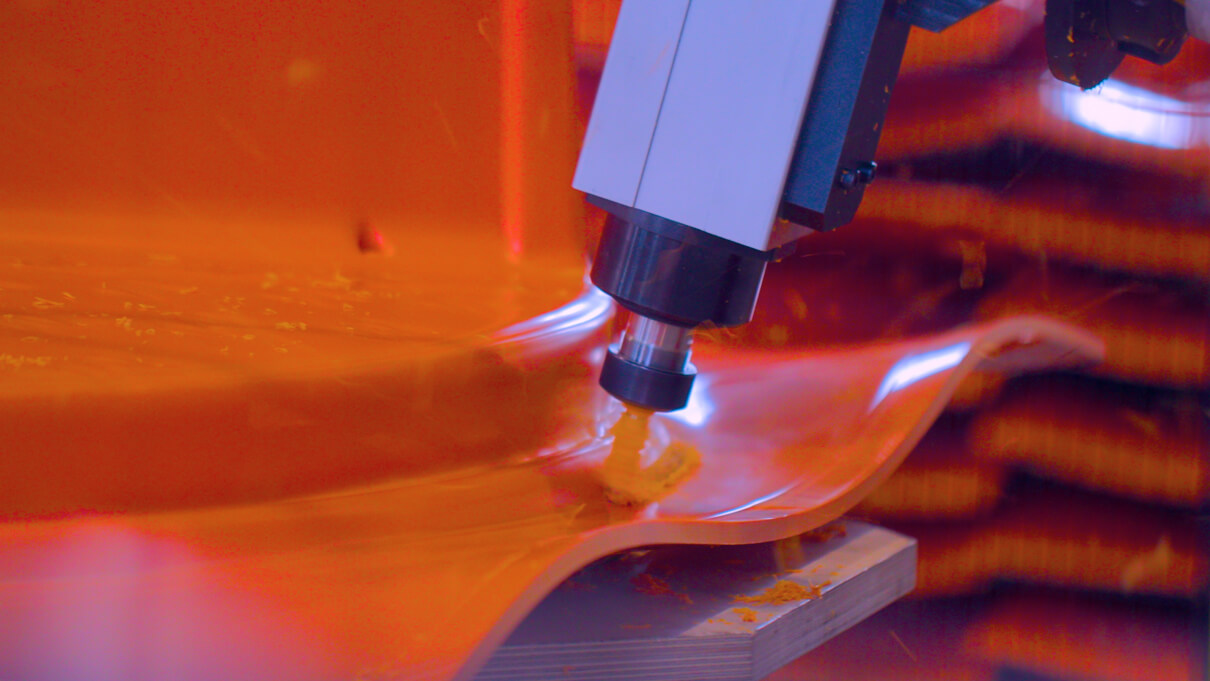
Vacuum forming is covering various industries
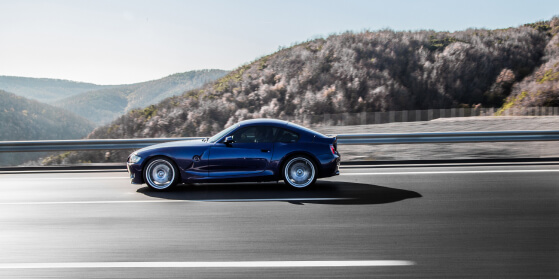
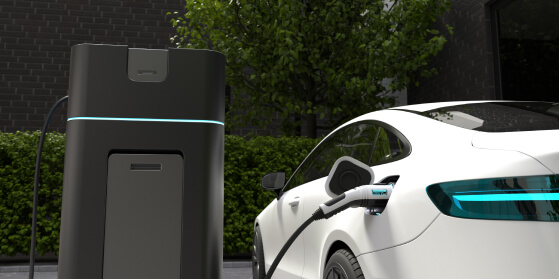
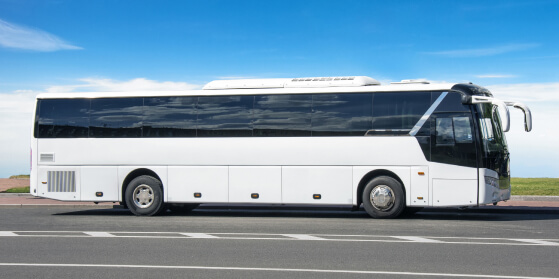
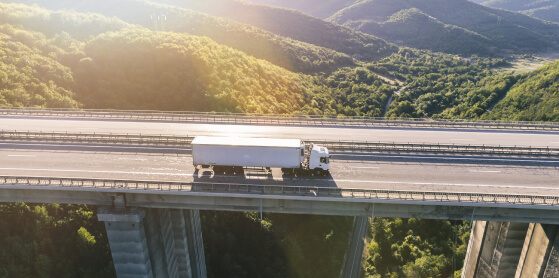
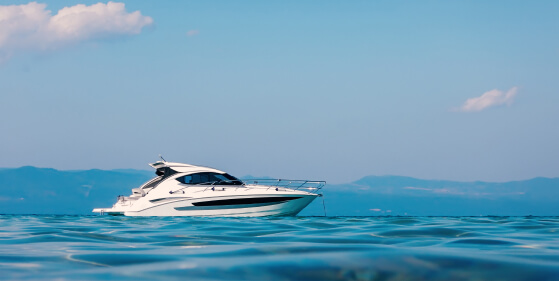
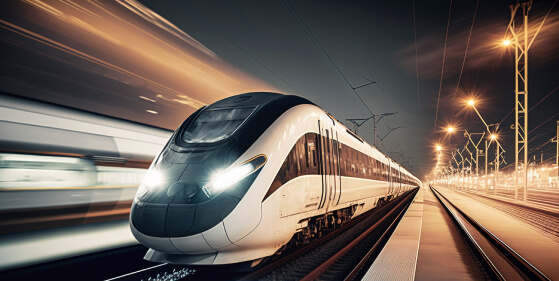
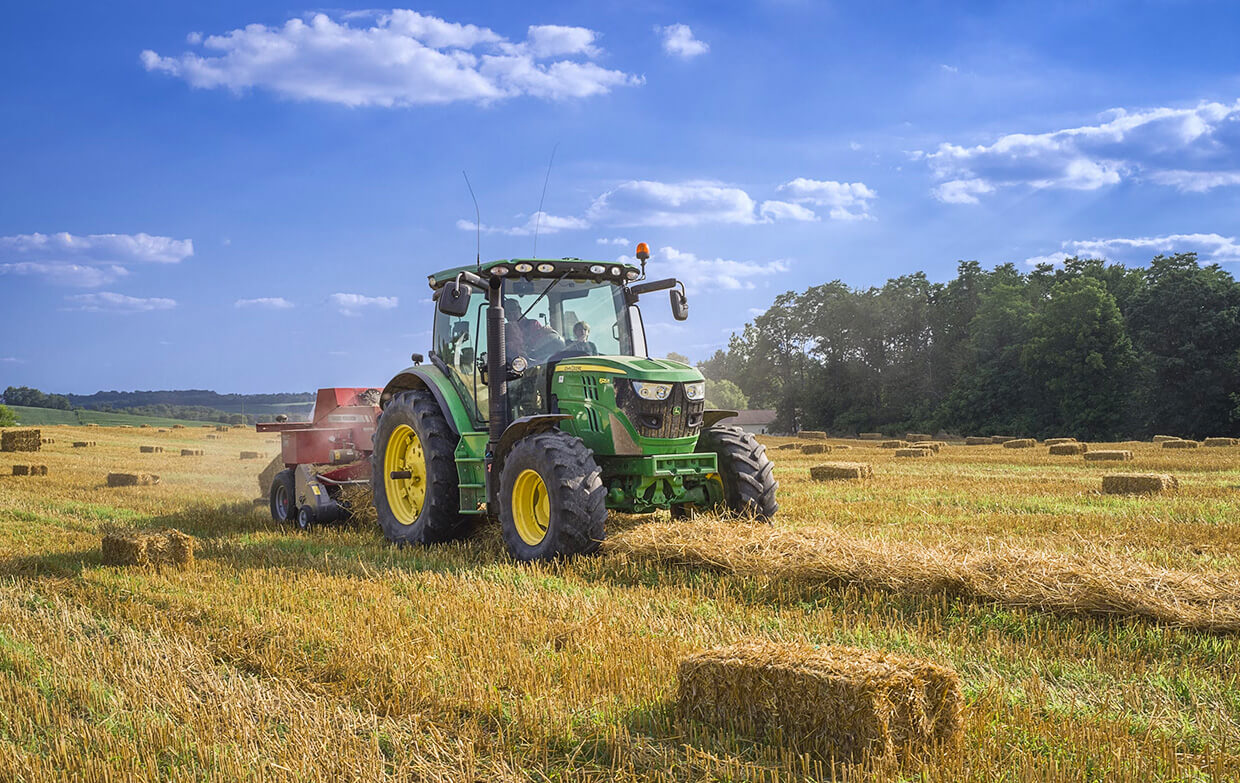